
Note, however, that this is the operating D MAX. We will in fact ignore this value ultimately, as we will be estimating D more accurately by another trick. This is clearly a “theoretical” estimate - implying 100% efficiency.

But the general procedure to handle such cases will become apparent as we study the other worst-case loss terms of the converter below.ĭ = V OR V OR + V INMIN = 128 128 + 127 = 0.5 ( f l y b a c k ) Generally, the core loss term, being such a small component of the total loss, is of no great concern to us, so we won’t even bother to do a numerical calculation here. That would be the input voltage extreme with a D closest to D =0.5. And we need to then do the worst-case core loss calculation at that end. Note: If for the Boost, the input range of the given application does not include the D =0.5 point, we need to identify which voltage end of the range provides a duty cycle closest to D =0.5. Note that from the duty cycle equation of Boost, D=0.5 corresponds to an input voltage equal to half the output. But the worst-case core loss for this topology actually occurs at D=0.5 (see the I AC curve for Boost in Figure 2.4). Similarly, for a Boost, we would also start the general inductor design calculation at V INMIN. But the core loss is a maximum at V INMAX. However, if we were doing the calculation for a Buck-Boost, our general inductor design calculation starts at V INMIN.

Therefore, calculating the core loss at V INMAX as we did in the previous example does coincidentally also give us the worst-case core loss. For a Buck, the general inductor design calculation above was carried out at V INMAX and that just happens to be the point at which the core loss is a maximum too. If for any reason, we are interested in knowing what the maximum core loss component of the total loss is, we should realize, looking back at Figure 2.4, that though the DC level may be going up as input voltage falls, the AC component (on which the core loss term depends) may actually be decreasing (or having an odd-shaped profile, as for the Boost).įrom Figure 2.4, we see that I AC increases at high-input voltages for both the Buck and the Buck-Boost, but not necessarily for the Boost. But that is because the I DC component of the inductor current is usually the dominant term. The point at which we are doing the inductor design usually gives us the worst-case temperature rise too. But this point may not be the worst-case for the other stresses in the power supply, and we need to start understanding that clearly now. The reason was that the inductor sees the highest peak current at this voltage end, so we have to “ensure” the magnetics design at these particular points (extremes). In the above so-called “general inductor design procedure,” we have actually been working at V INMAX for a Buck, and at V INMIN for a Boost or Buck-Boost. Sanjaya Maniktala, in Switching Power Supplies A - Z (Second Edition), 2012 Worst-case Core Loss As a rule of thumb, notwithstanding other considerations, optimum Q is obtained when l = 2 r. The diameter of wire that can be used will be limited by the length l of the inductor, which is specified in equation ( 1.3.7). For the time being let us just say that parasitic resistance in inductors is generally undesirable, so it is always a good idea to use the largest diameter wire possible in any given application. Q will be discussed in more detail in Section 1.6.
#Air core inductor calculator output voltage skin#
What the wire diameter does affect is the parasitic resistance, resulting from the skin effect, which impacts an important parameter called the “ Q,” of the inductor. This is because, to a first approximation, the diameter of the wire itself does not have a significant impact on the inductance of a single-layer wound inductor. Readers may note that the diameter of the wire does not appear in equation ( 1.3.7).
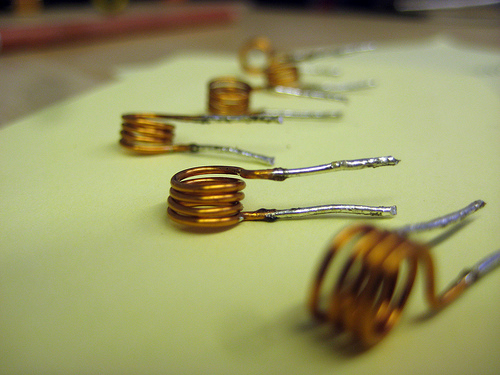
The formula ( 1.3.7) is an approximation that starts to become less accurate as l decreases below 0.67 r. Source voltage Inductance L1 Inductance L2 Output voltage This calculator requires javascript to function properly.L = Inductance in μ H l = Coil length in cm r = Coil radius in cm N = Number of turns V out is the output voltage and is measured in volt (V) CalculatorĮnter three values to calculate the remaining one. V in is the input voltage and is measured in volt (V) L is the symbol for inductance and is measured in henry (H). The output voltage can be calculated with the following formula: You can find more information about these here: You can also use other components like resistors and inductors. One of the inductors is connected from the input to the output and the other one is connected from the output to ground. Inductive voltage dividers are made out of two inductors. Electronics / Inductor / Inductive voltage divider Inductive voltage divider
